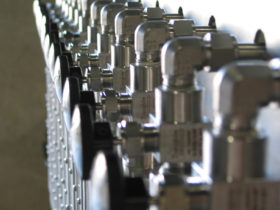
Specialty Equipment
SRU Tail Gas Diverter Valves
Tail Gas Diverter Valves are in the most severe service of all the actuated SRU valves. On their best day, TGVs are exposed to a combination of acid gases, high temperatures, and entrained liquid sulfur. Combine this harsh service with prolonged operation in a fixed position, and many TGVs are a recipe for Failure-on-Demand. PTI has developed a unique set of performance-enhancing features to keep your TGVs ready to roll when you need them most.
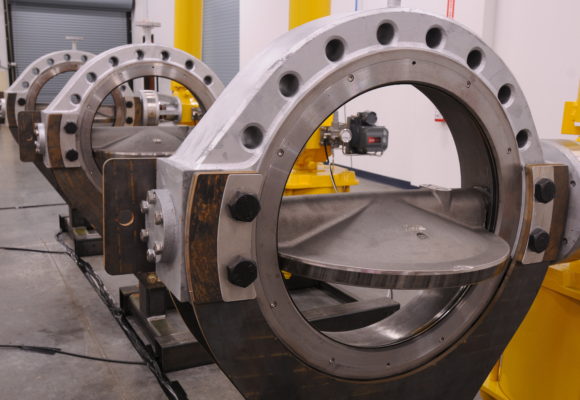
Principal Technology’s Tail Gas Diverter Valve Systems provide reliable automatic operation in your Sulfur Unit. PTI’s valves are specially designed for SRU tail gas service. Our engineers tackled the problem of tail gas valves by treating it as a critical operating “system” and not just a “valve.” Several great valve manufacturers offer high-performance valves but absent the complete system approach; even the highest quality HPBV will be challenged to operate on demand.
PTI’s Tail Gas Valve system tackles the following problems experienced by all SRUs:
- Temperature Management: Sulfur’s unique physical properties of a high melting point and an inverted viscosity curve make it challenging to keep in the sweet spot.
- Bearing protection: Bearings have a bad habit of sticking out in space and functioning as excellent heat sinks. Cold bearings condense and freeze sulfur at the worst possible location.
- Shaft Protection: If it’s stuck, just hit it with more torque. While that works in most applications, a sheared shaft in a Tail Gas Valve can turn a minor upset into a 3-day plantwide outage or curtailment.
- Performance Monitoring: The best-designed system in the world cannot overcome Murphy’s Law. Monitor and alert your operators of unseen upsets before they compromise the integrity of your Tail Gas Diverter Valves.
- Partial Stroke Testing: Operators need more than a smart positioner to perform partial stroke testing in an SRU. Hands-on Partial Stroke Testing allows operators to quickly and easily monitor your TG Valve’s performance and readiness for operation.
Our approach:
PTI Tail Gas Diverter Valve Systems tackle these common problems. We start with a high-performance butterfly valve* constructed from corrosion-resistant alloys and trims and add the following unique set of features and critical design elements:
- Temperature Management – Perhaps the single most significant factor in long-term TGV performance:
- Weld-on Integral Steam Jackets. Even with copious amounts of heat transfer cement, bolt-on steam jackets simply do not provide the intimate contact required to maintain the tight temperature control required in SRU TGV service.
- Heated Bearing Blocks. The horizontal shaft required for TGVs creates a challenge, how to get steam and condensate through the jacket without creating condensate pockets. PTI’s TGV design incorporates cross-bored bearing blocks allowing complete condensate evacuation. This design feature allows live steam to heat both the valve seat and bearings, keeping them above the sulfur freezing temperature.
- Steam Jacketed Piping – Around the TGVs… don’t cut corners. Steam Tracers and formed tube / strap-on steam jackets or tracers are fine in less critical areas of your SRU, but adjacent to the TGV, only use fully welded construction steam jacketed piping. PTI recommends a minimum of 3-5 pipe diameters up and downstream with plate-style flanges to allow steam contact immediately adjacent to the TGV flange.
- Reliable Steam and Condensate Systems. Tail Gas Valves need to have dedicated steam supply and condensate trap stations. Daisy chaining steam through your TGV system is tempting, but the added reliability of dedicated steam & condensate is cheap insurance.
- Steam heated valve shaft…. One thing not to do. The longevity of your TGV system will largely depend on how easy it is to maintain. Some manufacturers drill the valve shaft to apply steam directly. The drawbacks of this approach far outweigh the benefits.
First, most of the shaft is inboard of the pipe and valve body, where there is no benefit to added heat. Second, heating the shaft requires pipe and tubing swivels or flexible hoses to accommodate the moving assembly. Over time (often a very short period of time), these assemblies will leak and either need to be shut off or become a maintenance headache. In extreme cases, these steam leaks can mix with the process gases to form acid and greatly accelerate corrosion in the area.
- Bearing and Seat Protection – Keep it hot and keep it clean. Sulfur has a bad habit of finding a place to freeze. In addition to the tight temperature management described above, PTI’s TGV design includes laminated graphite packing, extruder rings, and a special disk seal system that keeps sulfur out of the bearings and meets ANSI Class VI shutoff criteria.
- Shaft Protection – As a result of the aggressive service, most Tail Gas Valves include oversized actuators; our system is no different. The shaft coupling, however, gets some added engineering attention. A sheared shaft is a great way to turn a minor upset into a multi-day repair. PTI’s coupling design includes engineered Woodruff keys designed to protect the shaft from exceeding its torque limit without compromising actuator torque output.
- Performance Monitoring – PTI designs our TGV systems to include continuous temperature monitoring at the most critical portion of the valve body. Our engineers performed rigorous finite element modeling to identify the region of the valve body most likely to suffer from excess temperature loss during upset conditions. By working closely with our valve manufacturers, we incorporate a drilled and tapped temperature port to continuously monitor this region of the valve body to detect upsets in the temperature maintenance system before it becomes a long-term problem.
- Partial Stroke Testing – Trust but Verify – The reliability of any instrumented system is significantly increased by performing regular function tests. PTI TGV systems include local jog-panels with manual lever shuttle valves that allow operators to quickly and easily partially stoke test your TGV to ensure your valve bearings and seats are ready to work when you need them.
Contact us about your Tail Gas Valve challenges. We routinely provide our TGV System in “Kit-Form,” allowing you to incorporate the TGV into your plant during an outage or revamp, or our engineers and designers can provide a skid-mounted Tail Gas Valve module complete with all steam tracing, condensate system, piping, insulation, and control wiring ready to plug-and-play in your unit.
related Specialty Equipment
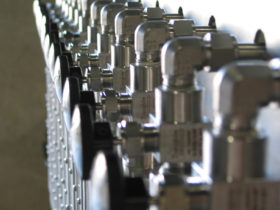
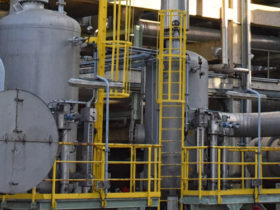
Amine Filtration Systems
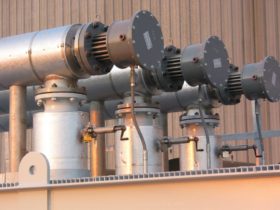
Electric Process Gas Heaters for Sulfur Recovery Units
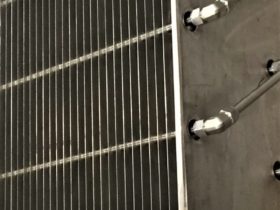
Entrained Sulfur Removal Elements – Heated ESRE™
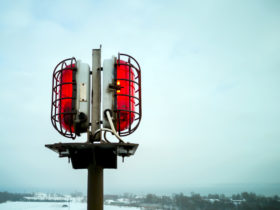
Hazardous Area Gas Monitoring
Low-Pressure Rich Amine Flash Drums (RAFD)
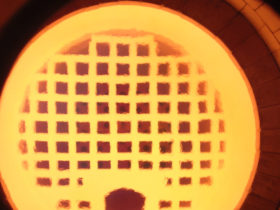
SRU Modified-Claus Process Burners
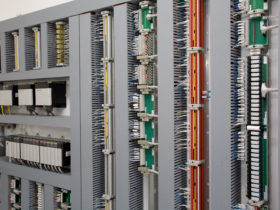
Sulfur Complex Burner Management Systems
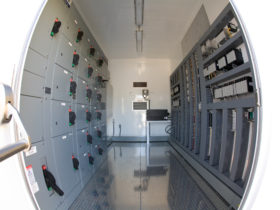
Sulfur Facility Process Safety and Control Systems
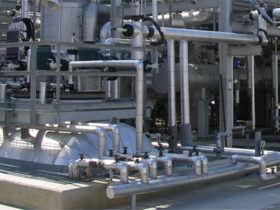
Sulfur Handling & Degassing
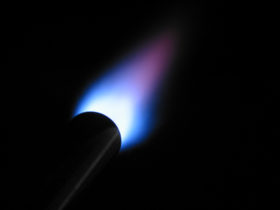