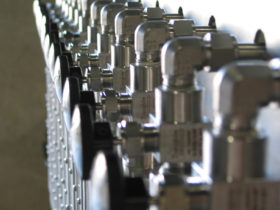
Specialty Equipment
Electric Process Gas Heaters for Sulfur Recovery Units
Electric gas heaters are a great option to replace traditional steam, hot-oil, indirect and direct-fired SRU Reheaters and Tail Gas Feed Heaters.
Electric heating can provide full-duty heating for small to mid-sized SRUs and Tail Gas Units or can be used as trim heaters downstream of traditional heat exchangers.
PTI pioneered using electric heaters in small-capacity SRUs in the early 2000s. Electric heating offers a unique advantage and significant cost savings over traditional SRU designs.
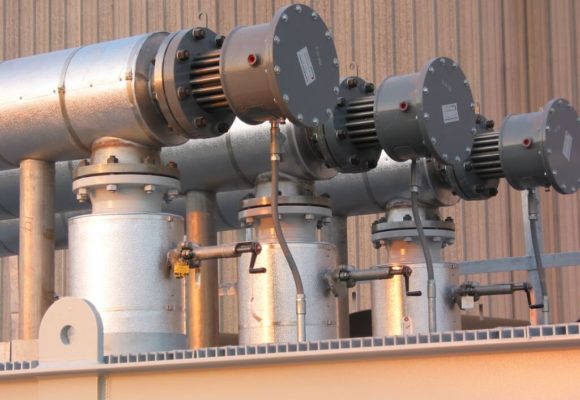
Using electric heaters in Sulfur service does, however, require a little more attention to detail than “clean” process heating applications. The system’s mechanical and piping design, carefully controlled heat flux, and process control targeted to the challenges of a sulfur environment are just a few of the design elements that PTI’s team can bring to your project.
Process Reheaters and Tail Gas Feed Heaters commonly used in SRUs and TGTUs were originally natural gas or refinery fuel gas direct-fired heaters. While direct-fired heaters are extremely simple and cost-effective, they often contribute to long-term operations headaches caused by sooting, excess air control, and are particularly vulnerable to process upsets.
Large facilities with significant utility infrastructure commonly replaced these heaters with steam and hot-oil heat exchangers. Both work well and eliminate sooting and excess air control challenges. However, these systems require additional capital costs associated with the piping and controls needed to operate these exchangers in sulfur applications. In the case of Tail Gas Feed heaters, 600+ PSIG steam is often required to provide adequate temperature for the Tail Gas Reactor.
PTI’s engineers pioneered the use of electric heaters in SRU and TGTUs in the early 2000s as many small/medium-sized facilities and other specialty processing plants expanded their sulfur unit operations or installed their first SRU and TGTU.
While electric heaters are common in many process industry applications, applying this technology in Sulfur service creates unique challenges. PTI’s design approach addresses each of these challenges.
- Metallurgy – Sulfur can, and often does, attack most carbon steel and low-alloy stainless. PTI manufactures both the electric heater and heater shells from alloys selected to resist sulfide attack.
- Heater Shell and Piping Design – As with many components used in Sulfur service, piping and equipment layout are critical to prevent cold-spots, pockets, and other flow disturbances that provide a location for sulfur to form, collect, or solidify. Addressing these concerns in our electric heater design is critical to provide the equipment longevity required in a continuous process operation.
- Redundancy – Short of full capacity online spares, which is an option, PTI carefully specifies the design of our electric heater bundles to incorporate spare elements that are available without the need to shut down the unit and take the equipment out of service.
- Heat Flux – “Clean” services can accommodate high heat flux from electric resistance heater elements; however, this must be tightly controlled in sulfur service to prevent hot-spots that can accelerate sulfur attack.
- Process Control – Simple, single-loop temperature control of electric heaters can cause unnecessary temperature excursions. PTI’s unique design approach tackles this challenge by coupling process feedback with direct electric heater sheath temperature control to curtail the heater demand during low flow process upsets.
- Process Safety – Unlike steam or hot-oil heaters, electric heaters are not temperature self-limiting. Our heater safety functions are designed to tackle this hazard by independently monitoring the heater sheath temperature to cut-out the power supply if hazardous temperatures are detected.
Contact our team to discuss how electric heaters may be a good option to upgrade your unit.
related Specialty Equipment
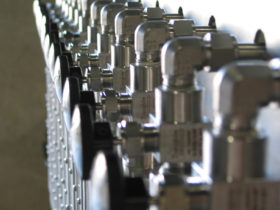
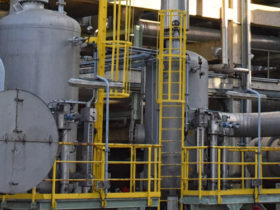
Amine Filtration Systems
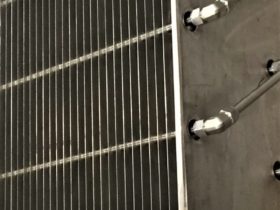
Entrained Sulfur Removal Elements – Heated ESRE™
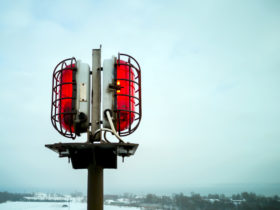
Hazardous Area Gas Monitoring
Low-Pressure Rich Amine Flash Drums (RAFD)
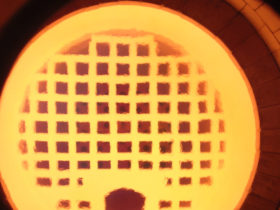
SRU Modified-Claus Process Burners
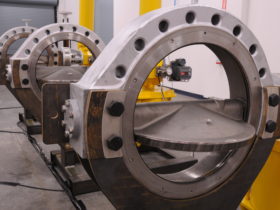
SRU Tail Gas Diverter Valves
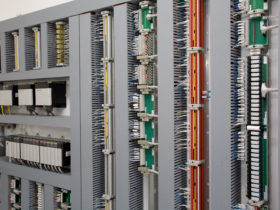
Sulfur Complex Burner Management Systems
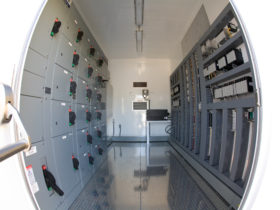
Sulfur Facility Process Safety and Control Systems
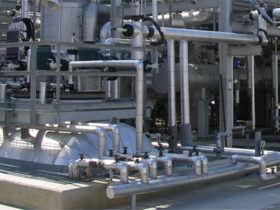
Sulfur Handling & Degassing
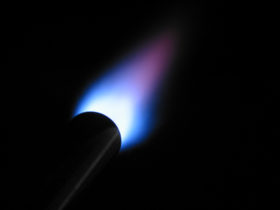